Melett Design Improvements
Due to homologation, once a design is approved by a vehicle manufacturer, the turbo OEM’s cannot deviate from this original approved design without seeking a revised approval, something the vehicle manufacturer may not be willing to retest due to associated costs.
Melett is not restricted by homologation and where possible incorporates improvements in the original design and uses upgraded parts.
Let’s look in detail at some examples of this:
BV/KP31/35/39 Thrust Flinger - Improved Twin Ring Design
All Melett KP35/39 CHRA’s are upgraded from single to twin ring comp end for improved sealing
- When the original KP35 turbo came out in the early 2000’s, it was a flatback designed compressor wheel with one piston ring groove on the flinger;
- The original design was prone to oil leaks at the compressor end as the piston ring seal wasn’t good enough;
- The upgraded twin ring is available on new complete OE turbos for most newer applications, Melett produce the twin ring flat back flinger to upgrade all old designs as well as new ones;
- At Melett, we build all our CHRA / Core Assemblies using a twin thrust flinger;
- We also produce both flat back and superback twin ring fingers, to replace the original designs.
BV/KP31/35/39 – 360° Thrust Bearings in place of 180°
- The original BV35, BV39, KP31, KP35 & KP39 thrust bearing was the 3 pad, 180 degree design;
- Due to the open thrust pad area oil retention was an issue;
- In newer OE turbo applications, the 180 degree design has now been phased out and replaced with the 360 degree design;
- This has resulted in better oil pressure and lubrication;
- Melett only use the 360 degree thrust bearing design in all BV35, BV39, KP31, KP35 & KP39 CHRA / Core Assemblies, giving the turbo longer life;
- A breakdown of the oil film will cause premature failure of the bearing system, often with no obvious signs of lack of lubrication or oil contamination.
Melett Part No. 1303-035-321
GT15-25 Thrust Bearings - Upgraded Thrust Design
In the beginning, there were two main types of GT15-25 turbo, those with a sintered steel 270° thrust bearing and those with a 360° stamped brass alloy thrust bearing.

- Sintered Steel
- Copper impregnated
- Used mid 90’s-2003
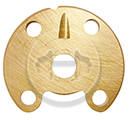
- Stamped brass alloy
- Used until 2002-2006
- Small thrust pads
Melett’s replacement for both of these bearings is 1102-015-324
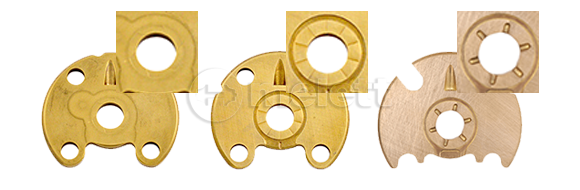
Original 6 pad design
Original 10 pad design
First Generation
Newer large pad design more resistant wear and thrust force
Second Generation
Key Points:
- Garrett are unable to make any changes due to Homologation
- Melett only use the latest design in all CHRA
- Hot forged design – not sintered!
In 2003-2005 Garrett moved to using a hot forging process to improve accuracy in manufacture (Hot forging produces a more robust blank by re-forming the grain in the material into the finished shape and also allows the use of a high strength alloy). A harder material with silicon, which acted like a non-stick surface, was then used and they also altered the thrust pad designs for different run-up requirements.
Melett uses the 1102-015-324 thrust bearing in all GT15-25 core assemblies
There are several more features on the thrust bearing which are important to the operation and life of the turbo, these include: oil pockets, size and finish and even what appear to be scratches on the surface on the GT15-25. These are actually designed into the product to increase the surface retention of oil, which will hold the oil on the thrust bearing for longer. This helps reduce wear on cold start-ups.
K03/4 Thrust Bearing - Melett Hot Forged vs OE Stamped
At Melett, we understand the different methods used to produce thrust bearings and where possible improve the original design used. The original K03/4 thrust bearings are produced using a stamped strip manufacturing process, however, Melett replacement K03/4 thrust bearings are produced from a hot forged method, creating a much stronger thrust bearing.
So, what does this mean?
Stamped Strip – Involves stamping the initial blanks out of a strip of brass material and is used for smaller thrust bearings. This method limits the strength of the material as this has to be weighed against the life of the stamping tool, an increase in strength in the material causes a massive reduction in tool life.
Hot Forging – is a more recent method of producing thrust bearings. A high tensile billet of brass material is heated to near melting and then pressed into a die to create a forged blank. This has the advantage that the material grain is pressed into the shape of the finished product and the material used can be much higher strength than stamped material. The recent turbo developments have increased pressures on the thrust surface, as such, many turbo manufacturers have moved to hot forged thrust bearings over the past decade. Where possible, Melett uses the hot forged method as we believe it produces a superior product.
Melett only uses the latest thrust bearing design in all CHRA.
GT15 Journal Bearings – Original Designs
The GT15 journal bearings have improved over the years. They started with Melett part numbers 1102-015-100 (slender shaft) and 1102-015-101 (straight shaft). The differences in these bearings are shown below.
1st Generation slender shaft bearing with smaller lands.
Provides less resistance meaning increased run-up speeds.
2nd Generation straight shaft bearing with large lands,
used predominantly on larger applications.
There are 2 original designs for the GT15 journal bearings with the most important differences being the length of the internal bearing surface.
GT15/17 slender shaft turbos:
Original GT15 bearing (OE No. 433123-0002 / Melett No. 1102-015-100):
- smaller internal bearing surface length at the compressor side;
- larger length at the turbine side.
On new generation turbos, the improved bearing (Melett No. 1102-015-104):
- internal bearing surface has a larger length on both sides;
- the material is different;
- the oil grooves and holes are slightly different.
This bearing is also used with straight shaft turbos in the GT15-17 range and can be used to replace the old style bearing.
GT20/25 straight shaft turbos:
On the larger turbos in the VNT range:
- the bearing (Melett No. 1102-015-101) has a longer internal bearing surface length (than the 1102-015-104), at both sides;
- on 2nd generation turbos, this bearing has not changed dimensionally but the material has been improved.
GT15 Journal Bearings – Improvements:
The GT15 journal bearings were improved to increase the size of the lands and also to improve the brass alloy used for the bearings. As with the thrust bearings this contained silicon for improved lubrication (similar reason for the use of Teflon in non-stick pans).
2nd Generation slender shaft bearing with larger lands than previous version.
Designed for low viscosity oils. Replaces 1102-015-100 bearing.
This information is meant as a general guide. It is important to identify which bearing is in the turbo when stripping and replace this with the same style. The easiest way to identify the bearing is by measuring from the side face to the start of the internal bearing surface.
GT15 Seal Plate – Extra Strengthening Ribs
Seal plates are prone to failing around the compressor wheel diameter, to improve the strength the Melett 1102-015-300 seal plate has been designed to incorporate extra strengthening ribs to help prevent failures.
GT15-25 Slender Shafts – Increased Radius to Reduce Stress
Common turbo failures such as overspeeding can cause severe fatigue to the shaft and wheel. Signs of fatigue include partial loss of blades caused by the constant flexing of blades beyond the designed parameters. Fatigue is a mode of failure not the cause.
Traditionally, a shaft and wheel has an open back with a slender or straight shaft. To strengthen the turbine wheel, Melett has developed a full back shaft and wheel solution, which reduces the risk of fatigue on the inducer diameter.
GT15 Nozzle Assembly – Solid Vane Design
During the design review of the GT15 nozzle assembly, Melett Engineers analysed failure modes of many units. They concluded, the preferred route for the turbo aftermarket was the solid vane design for the 753420-* GT1544V nozzle ring, rather than the original welded strip metal design. This provides a stronger repair solution and allows you to offer your customers an upgraded repair.